Production process of lithium iron phosphate battery cells
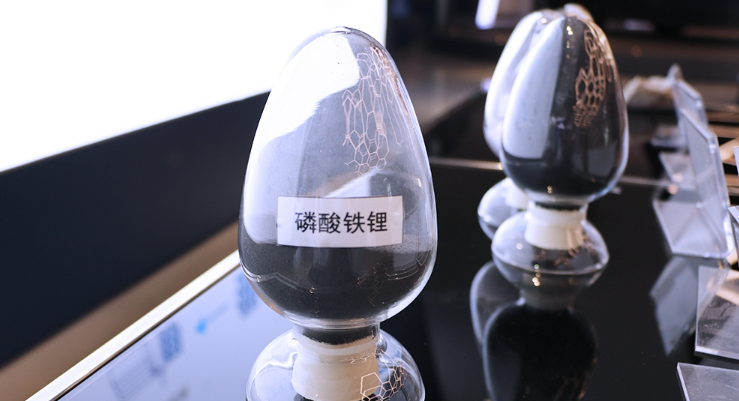
The production process of lithium iron phosphate battery cells involves several key steps, including raw material preparation, electrode manufacturing, battery cell assembly and testing. Each manufacturer is slightly different, and it is mainly divided into the following steps: material preparation - homogenization - coating - rolling - slitting - baking - winding - shelling - laser welding - baking - liquid injection - pre-charging - sealing - cleaning - aging - full inspection - warehousing - shipment.
The following is our summary of the main links and detailed steps of Guoxuan lithium iron phosphate battery cell production process:
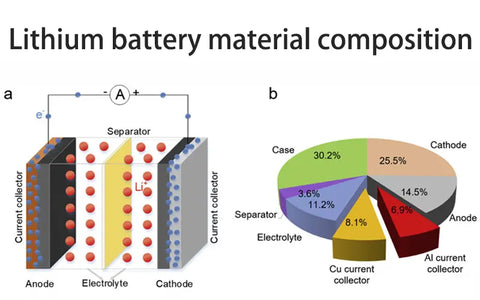
1. Raw material preparation
Positive electrode material preparation:
Lithium iron phosphate (LiFePO₄) is used as the positive electrode active material.
The material undergoes processes such as grinding, mixing and sintering to ensure that its particles are uniform and the particle size is moderate.
Negative electrode material preparation:
Mainly use artificial graphite or natural graphite, which is spheroidized, coated and screened to ensure that it has high conductivity and good cycle stability.
Electrolyte:
Prepare an electrolyte containing lithium salt (such as lithium hexafluorophosphate LiPF₆) and solvent (such as ethylene carbonate EC, dimethyl carbonate DMC) to ensure battery ion conductivity.
Separator:
Choose polyolefin (PE or PP) separator or ceramic coated separator to ensure heat resistance and mechanical stability.
2. Electrode manufacturing
Coating:
Use positive and negative electrode slurry evenly on aluminum foil (positive current collector) and copper foil (negative current collector).
The slurry is made of active material, conductive agent (such as carbon black or conductive carbon) and binder (such as PVDF).
Drying:
The coated pole piece is dried at high temperature to remove the solvent, ensuring that the material is evenly attached and there is no residual solvent.
Rolling:
Use rolling equipment to compact the pole piece to increase the density and conductivity of the material.
Cutting:
Cut the positive and negative electrode pieces according to the specifications of the battery cell to ensure accurate size and smooth edges.
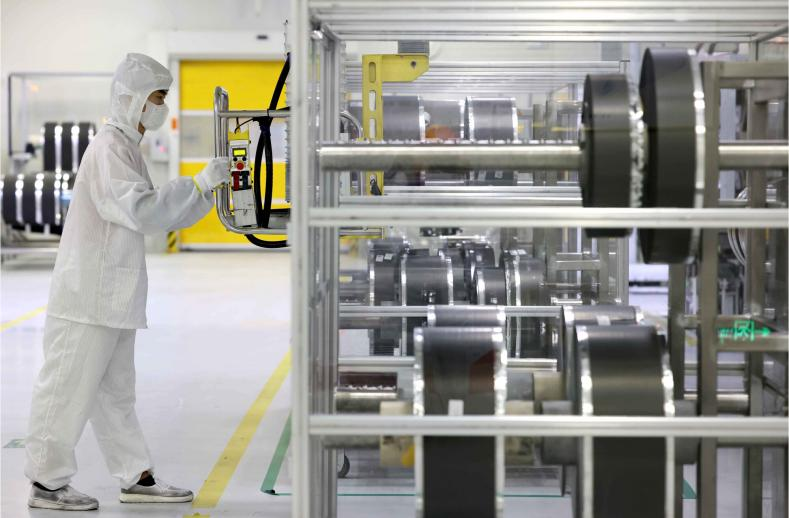
3. Cell assembly
Lamination or winding:
The positive electrode sheet, negative electrode sheet and separator are laminated or wound according to the design specifications. Lamination is suitable for square batteries, and winding is suitable for cylindrical batteries.
Ensure the alignment accuracy of positive and negative electrodes and separators to avoid short circuit risks.
Injection:
Inject electrolyte into the assembled cell to ensure that the electrolyte is evenly distributed.
Packaging:
Package the cell after injection. Soft-pack batteries are packaged with aluminum-plastic film, while square batteries are packaged with aluminum shells.
Activation:
The cell is initially activated through charging and discharging to form a stable SEI (solid electrolyte interface) film to optimize the performance of the battery.
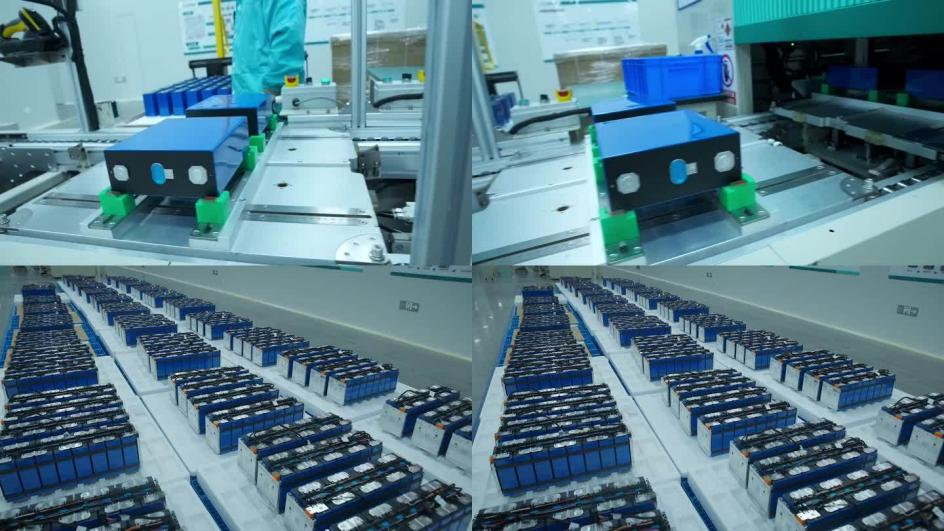
4. Inspection and testing
Appearance inspection:
Check whether there are defects on the surface of the cell, whether the welding is firm, and whether the size meets the requirements.
Electrical performance test:
Including tests of parameters such as capacity, internal resistance, cycle life and self-discharge rate.
Safety test:
Perform tests such as needle puncture, extrusion, overcharge and over discharge to ensure that the safety performance of the cell meets industry standards.
5. Subsequent processing and packaging
Capacity division and grouping:
Screen and group the cells according to their voltage, capacity and internal resistance to ensure consistency.
Factory inspection:
Test the battery, including electrical performance and environmental adaptability tests (such as high and low temperature tests, vibration tests).