GBE Lithium Forklift Battery, Higher Performance, Embrace Lithium Battery Technology, Enable the Future with Lower TCO: Material Handling
Forklifts are the workhorse of material handling in many industries, revolutionizing the way goods are transported in industries such as manufacturing, warehousing, distribution, retail, and construction. As we enter a new era of material handling, the future of forklifts will be marked by key advances, lithium battery technology. These technologies are expected to improve the performance, efficiency, sustainability, and cost-effectiveness of forklifts.
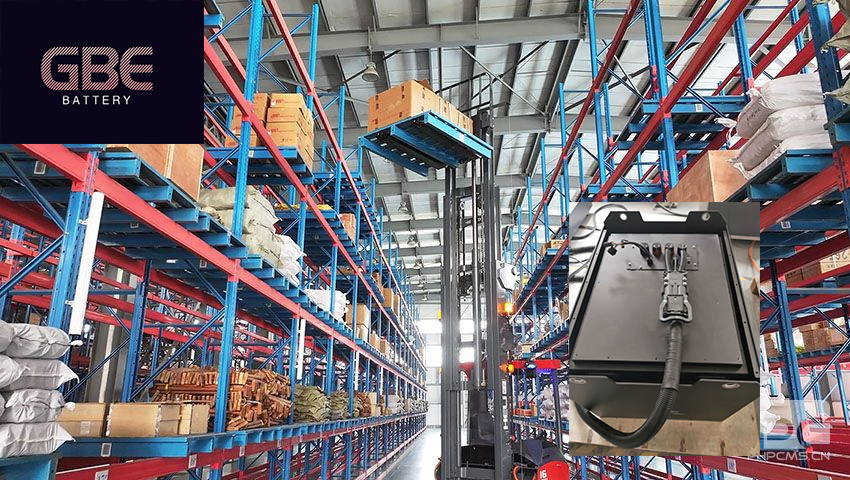
Battery Type: Choose Lithium Batteries over Lead-Acid Batteries
For many years, lead-acid batteries have been an effective solution for electric forklifts and have dominated the market. With the growing demand of the global supply chain, most material handling industries must optimize operations, reduce costs, ensure on-time delivery, and pay attention to environmental protection. Compared with traditional lead-acid battery solutions, forklift lithium batteries can meet these challenges.
Its advantages include: Higher energy density: Storing more energy without increasing size makes lithium battery forklifts more flexible in operations that require close operation. Fast charging, no recharging required: No memory effect, can be recharged during breaks and between shifts. For industries that operate multiple shifts per day, it can improve equipment availability and maximize uptime.
More stable performance: The voltage at all discharge levels is stable, which can achieve consistent performance without sudden power drops. No hazardous substances: safe and environmentally friendly. No need to build a dedicated battery room, nor to purchase HVAC and ventilation equipment. Almost zero maintenance: No regular watering and daily inspections are required. No need to remove the battery from the forklift for charging. Reduce the need for battery replacement, battery maintenance frequency and labor costs.
Longer service life: With a longer cycle life, a battery can be used for many years and provide reliable power.
Enhanced safety: The intelligent battery management system (BMS) supports real-time monitoring and multiple safety protections.
GBE has always had high quality requirements for forklift lithium batteries, which is reflected in all stages of our quality control.
The quality control of forklift lithium battery packs is mainly concentrated in the battery cell, pack assembly, and BMS (battery management system). Specifically, it is necessary to strictly test the raw materials, production process, and battery cell parameters (voltage, internal resistance, capacity, etc.) of the battery cell, and ensure the consistency of the battery cell group. During the pack assembly process, attention should be paid to insulation, connection, mechanical strength, waterproof and dustproof, thermal management and other issues. The quality control of BMS includes testing and verification of SOC, SOH, charge and discharge protection, balancing, temperature monitoring and other functions to ensure the safety, reliability and service life of the battery pack.
The following is the detailed content of the quality control of forklift lithium battery pack:
1. Battery cell quality control:
Raw material quality control:
Ensure that the quality of raw materials used in lithium batteries (such as positive electrode materials, negative electrode materials, diaphragms, electrolytes, etc.) meets the standards and avoid the use of inferior or unqualified materials.
Production process control:
Strictly control the production process of battery cells, including ingredients, coating, rolling, film making, winding, packaging, injection, formation and other links to ensure that each link meets the process requirements.
Battery cell parameter consistency control:
Strictly screen and group the parameters such as voltage, internal resistance, capacity, self-discharge rate of the battery cells to ensure the consistency of the battery cells and avoid battery pack performance degradation or safety problems due to differences in the battery cells.
Battery life test:
Carry out cycle life test on battery cells to evaluate their performance degradation under different working conditions, and provide reference for the design and service life of battery packs.
Battery safety test:
Carry out safety tests such as overcharge, over discharge, short circuit, and high temperature on battery cells to ensure that the battery cells can remain safe and reliable under various extreme conditions.
2. Battery pack assembly quality control:
Insulation performance test:
The insulation resistance between the components inside the battery pack and between the battery pack and the external shell must meet the standards to prevent leakage and short circuit.
Connector quality control:
Ensure that the connectors inside the battery pack (such as poles, wires, connectors, etc.) are reliably connected to avoid poor contact or looseness that leads to increased resistance or short circuit.
Mechanical strength test:
The battery pack needs to have sufficient mechanical strength to withstand mechanical stress such as vibration and impact to avoid failure of the battery pack due to mechanical damage.
Waterproof and dustproof performance test:
Forklifts usually work outdoors or in harsh environments. The battery pack needs to have certain waterproof and dustproof properties to avoid short circuit or corrosion due to water or dust ingress.
Thermal management system test:
The battery pack needs to have a good thermal management system inside to ensure that the battery temperature remains within a safe range during operation, avoiding overheating or overcooling that may cause performance degradation or safety issues.
PACK assembly process verification:
Ensure that the assembly process is reasonable and avoid quality problems caused by human factors.
3. Battery management system (BMS) quality control:
SOC (State of Charge) estimation accuracy test:
Ensure that the BMS can accurately estimate the remaining power of the battery to avoid overcharging or over-discharging.
SOH (State of Health) estimation accuracy test:
Ensure that the BMS can accurately evaluate the health status of the battery and provide a reference for battery maintenance and replacement.
Charge and discharge protection function test:
Verify whether the BMS's overcharge, over-discharge, overcurrent, short circuit and other protection functions are effective, and ensure that the battery can operate safely under various working conditions.
Balance function test:
Verify whether the BMS's balance function is effective, ensure that the voltage between the cells inside the battery is consistent, and avoid battery performance degradation or shortened life due to voltage imbalance.
Temperature monitoring and protection function test:
Verify whether the temperature monitoring and protection functions of BMS are effective, and ensure that the battery can take timely protection measures in the case of over-temperature or under-temperature.
Data communication and recording function test:
Verify whether the data communication and recording functions of BMS are normal, so that users can understand the operating status of the battery and perform fault diagnosis.
BMS software and hardware compatibility test:
Ensure the compatibility of BMS software and hardware to avoid the battery pack from not working properly due to software or hardware failure.
BMS aging test:
Perform a long-term simulated working condition aging test on BMS to evaluate its long-term reliability and stability.
BMS safety test:
Perform a safety test on BMS to ensure that it can remain safe and reliable under various abnormal conditions.